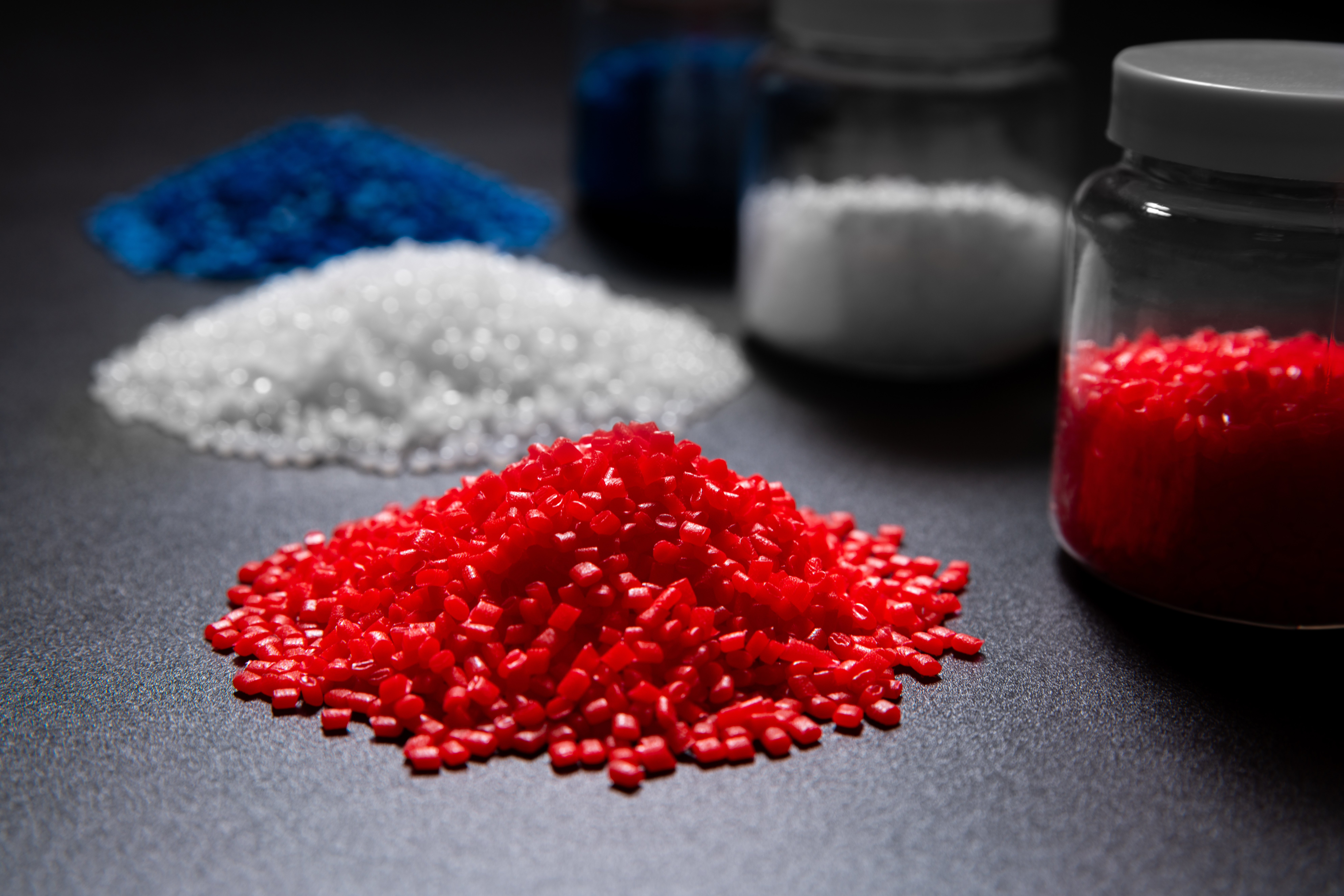
In the chemical processing industry, precise particle size reduction requires robust, reliable equipment tailored to the task. Size reduction and screening systems are integral to nearly every chemical application, ensuring the efficient preparation of materials for further processing. Standard chemical processes rarely achieve the exact particle dimensions required, which is why durable, high-performance equipment is essential to augment these reactions and deliver consistent results. Built to withstand rigorous operational demands, these systems are designed with longevity and precision in mind, reflecting a deep understanding of the complexities of chemical processing.
The Application of Size Reduction in Chemical Processing
Physics provides a clear explanation for the critical role of size reduction in chemical processing. Larger, coarser particles inherently possess limited surface area, reducing their ability to react efficiently. In contrast, smaller, finer particles offer significantly enhanced surface area, promoting effective chemical bonding. For this reason, particle size reduction is an essential step in virtually all chemical processing workflows.
To achieve consistent and efficient results, size reduction equipment must be designed and engineered with precision. Robust and reliable machinery ensures the quality and uniformity of the end product, a cornerstone of successful chemical processing operations. While optimizing chemical reactivity is the primary purpose of size reduction, this process also serves additional objectives, reflecting its versatility and importance in the industry.
Application of size reduction on chemicals also:
- Improves mixing of chemical ingredients by making them more uniform in both shape and size.
- Enhances adsorption by exposing greater amounts of surface area.
- Improves solubility, as smaller particles dissolve faster.
- Makes handling easier as smaller particles flow better, while also taking up less space during transport or storage.
Modern size reduction equipment is vital for dealing with processing challenges that can limit throughput in a chemical processing plant. Regardless of the application of size reduction methods, the industry often needs custom solutions for breaking down abrasive and toxic substances. For this reason, chemical processing companies often require heavy-duty size reduction equipment made from special alloys to enhance durability, or with protective surface coatings like tungsten carbide, hardfacing, or a ceramic coating.
Production in a chemical processing plant can be greatly affected by not breaking down material to the correct particle size. Reduction equipment offers a solution for chemical processing applications. Size reduction targets can be more easily achieved with the utilization of modern machinery with monitoring systems that can additionally measure distributions to ensure greater consistency and yields.
Size Reduction Equipment from S. Howes for Chemical Processing
S. Howes manufactures various types of size reduction equipment and other apparatus used by the chemical industry. Our company also manufactures continuous mixers and can assist with sizing reduction equipment for systems in the sector.
Specialized size reduction equipment made by S. Howes for chemical processing includes:
- Lump breakers: Designed to break down large blocks of chemicals for further downstream processing or transport, these can be placed in-line to make material particle sizes more manageable.
- Power graters: Used for application of size reduction processes in chemical processing, its low paddle speeds, minimal horsepower requirements and robust design make this a cost-effective choice.
Additionally, the Carrier Production Equipment Group (CPEG) Innovation Center allows processing companies to test new designs and processes before full production begins. To learn more about our size reduction equipment and other machinery used to optimize the processing of chemicals, contact S. Howes today.