Pancake Mixing System
The Process Challenge
S. Howes, Inc. was approached by a food processor to design a system to automate the previously labor-intensive mixing and bagging of pancake mix. Operations were constrained by 11-foot-high ceilings.
The Solution
S. Howes, Inc. designed and constructed an enclosed sanitary system that included a bag-dump station directly connected to a sanitary double ribbon mixer. Here, ingredients were mixed and transferred to a split-tube conveyor and surge hopper, before the product passed through a custom-designed conveyor into a bagging station.
Components
- Bag Dump Station mounted on the blender
- S-366 Double Ribbon Blender
- 6′ Split tube Screw Conveyor
- Surge Hopper
- 4′ Tubular Screw Conveyor with cleanout access doors
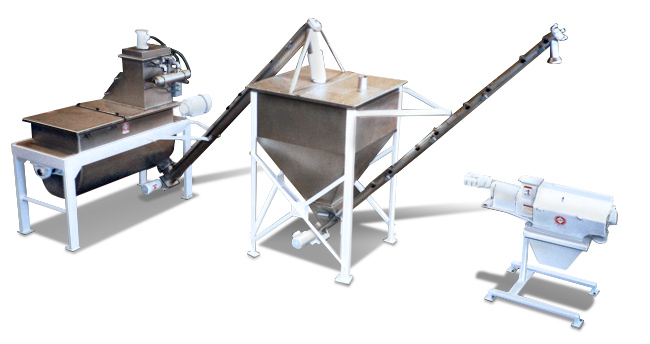
The Result
The closed system was fully automated, reduced labor costs, improved product consistency, and was built to accommodate all height constraints and sanitary specifications. This system could mix and bag 3,600 lbs. of pancake mix per hour.