Food Ingredient Unloading & Conveying System
The Process Challenge
A food manufacturer was expanding its operations and contacted S. Howes to design a conveying system to automate and increase the volume of spices it could process.
The Solution
S. Howes’ solution started with a bulk bag unloader that dispensed material into a conical hopper that fed the product into a 20-foot screw conveyor before the product entered a bagging system. The spice mix was salty and dense, which made it very difficult to convey. An agitator in the hopper was necessary to ensure a smooth and consistent feed into the screw conveyor.
Components
- Flexible Bulk Bag Unloading Station
- Support Framework
- 22 cu. ft. Capacity Hopper
- Hopper Agitator
- 6″ Diameter Screw Conveyor
- Consolidated Control Panel
Photos and drawings are not intended to show or suggest use or non-use of any operator protection systems.
The Result
The S. Howes’ system enabled the company to increase production and resulted in a more consistent and efficient transfer of food ingredients.
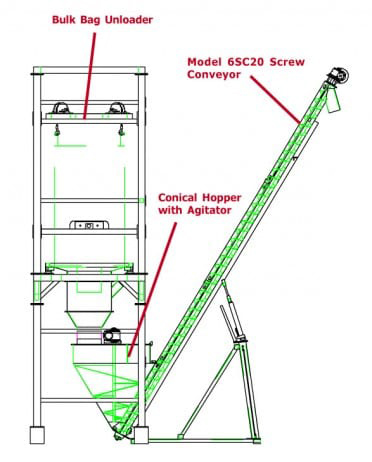