Drill Tailings Recovery and Solidification
The Process Challenge
Drilling for natural gas and oil in the northern states will grow inexorably over the next few decades. New environmental regulations imposed by state environment protection agencies, such as the PADEP, now address the disposal of drilling fluids. These new regulations can significantly increase an energy company’s drilling budget. Southern states have begun adopting similar regulations as an alternative to the open-pit disposal approach for drill tailings.
The Solution
S. Howes, with significant input from the operator and energy company, designed and built a closed-loop solids control system to solidify and neutralize residual drilling cuttings. S. Howes designed a system that greatly reduces the amount of haul-off and over-bulking of cuttings by utilizing a pugmill unit to process the drill cuttings. Unlike many other service providers attempting to develop similar systems, our setup processes air and mud-drilled cuttings without rigging up or down more equipment. The unit is entirely self-contained, and cuttings have no time to be transferred over open ground.
The auger tank sits underneath the rig’s primary shakers and captures the cuttings as they fall off the shaker slides. Once inside the auger tank, cuttings are conveyed via dual screws and then up into the pugmill by the incline auger. The pugmill consists of dual counter-rotating paddle augers that blend wet cuttings simultaneously with lime or other bulking agents. The lime comes from a 30-ton portable silo. It is equipped with a dust house for loading, and the filters can be purged with air if needed. It has a 30-ton capacity, which allows you leeway between refills of the pneumatic trucks, which generally run around 22 tons.
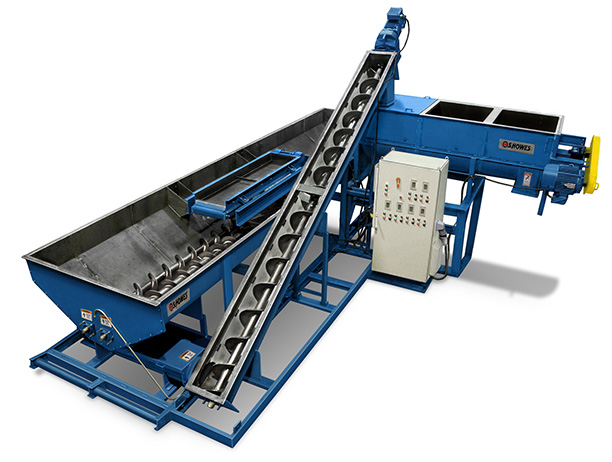
The bulking agent is augered into the pugmill to mix with the wet cuttings. A VFD control panel controls all the augers, so the drying agent can be administered depending on the wetness of the drill cuttings. This helps allow adequate bulking and controls the troublesome over-bulking associated with mixing with an excavator. A centrifuge stand can also be mounted over the auger tank to process those solids.
This particular operator was drilling the 17 1/2” surface hole with water-based spud mud and discharging it directly into the auger tank for solidification with the pugmill. Depending upon the wetness of those cuttings, the VFD augers could be synced with the lime silo for the appropriate bulking. The product is then discharged into a 20-yard roll-off container for shipment to a landfill. After running 13 3/8” casing, we processed the 12 ¼” and 8 ¾” vertical air sections of the hole. The operator had a shale gas separator rigged directly in front of the auger tank, discharging solids into it, and the tank was plumbed for a trash pump to circulate water to eliminate dust. Finally, to kick off the curve section on synthetic oilbase (SOBM), we have a secondary drying shaker that mounts inside the auger tank for that portion of the hole. The effluent is pumped into the centrifuge for processing and reuse. The fluid recovered can also be blended with unweighted slurry in a whole mud dilution. This minimizes the volume lost to the centrifuge and helps the mud retain its chemical properties while maintaining an appropriate low-gravity solids content. Options for fluid recovery can be tailored to the customers’ specifications.
The assembly of the unit is fairly simple and consists of only 5 pieces. It has a very small footprint in the backyard, which is helpful on multiple well pads where space restraints are an issue.
The Result
In summary, the system benefits the drilling company by:
- Allowing the operator to use one setup to process air and mud cuttings
- Reducing overbulking and lowering tonnage by 1/3 compared to that of mixing with an excavator
- Reducing bulking significantly lowers trucking costs, disposal costs at the landfill, and the amount of bulking agent needed to process cuttings.
- Eliminating cuttings being transferred over open ground because it is a self-contained unit
- Creating virtually dust-free, consistently mixed cuttings
- Creating an environmentally friendly solution in today’s ever-evolving eco-conscious oilfield