Conveying and Metal Detecting
The Process Challenge
A national spice company had experienced an increase in demand for a particular product. The production line was in a makeshift configuration to meet the new demands of the product temporarily. The spice was manually weighed directly from the mixer into bags. Weight accuracy was an issue, as well as the potential for metal particles in the food product. The operation required changing product mixes frequently. Therefore, ease of cleaning the system needed to be considered in the design of the units. The customer asked S. Howes to design and build a complete system to meet their multiple processing requirements.
The Solution
S. Howes proposed a high-quality sanitary turnkey system where the user could control all aspects of the process and easily clean the unit for quick turnaround. Emphasis was placed on a design that could be thoroughly cleaned. A portable, inclinable split-tube conveyor and hopper fed an integrated metal detector. A weight scale was attached below the metal detector to measure the product accurately before final packaging. High-quality, polished 316 stainless steel was used for all materials.
Components
- Two 6SC10
- Two 6SC13
- Two Metal Detectors
- Four Control Panels
- Two Weigh Scales
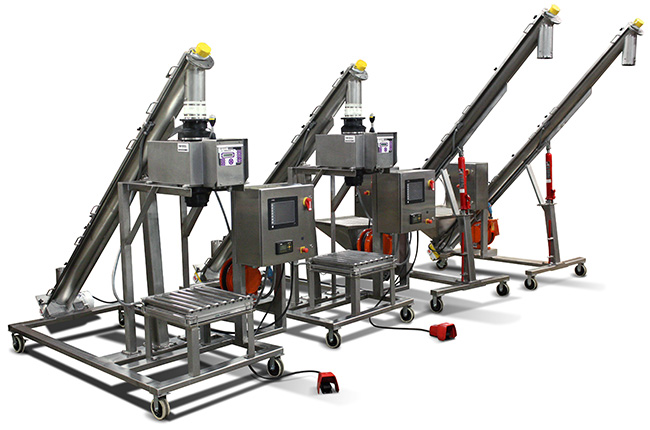
The Result
The Split Tube Conveyors with control panels delivered a more automated system that featured a sanitary design for quick cleaning.