Continuous Mixer & Reactor
The Process Challenge
A major international chemical manufacturer needed to replace an existing reactor with one that could double capacity and reduce maintenance. The process continuously blended a dry granular material with a hot strong acid solution and discharged it horizontally into a kiln. The chemical reaction allowed the evolution of an acid gas that could not mix with air.
The Solution
S. Howes proposed a specially modified version of the C-121 continuous mixer with standard, independently adjustable, replaceable paddles along with several adaptations:
- Alloy-20 construction to stand up to the high-temperature acid
- Replaced the traditional U-style body with a Tubular body to eliminate covers
- Eliminated discharge end bearing to allow direct discharge into the kiln
- Supported shaft with twin drive-end bearings and custom hanger bearing
- Custom mechanical shaft seal using engineered resins selected for compatibility
- Incorporated spay nozzles to provide highly efficient distribution of the acid
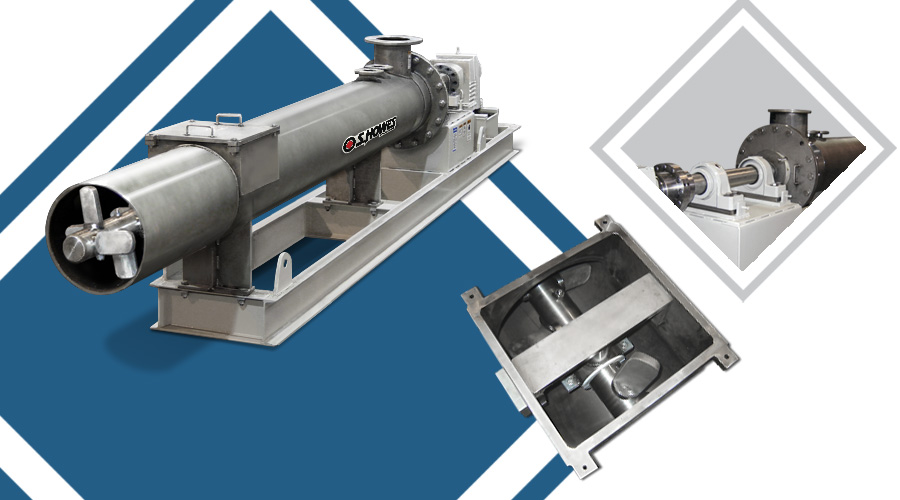
The Result
S. Howes successfully achieved the goals of the customer:
- The desired increase in production rate was achieved using the combination of the spray nozzles with the superior mixing performance of the S. Howes traditional and time-proven design
- The customer can replace individual paddles with basic tools instead of continually swapping repaired agitator assemblies.
- The mixer had a slightly smaller footprint and required no increase in power to achieve the desired results.