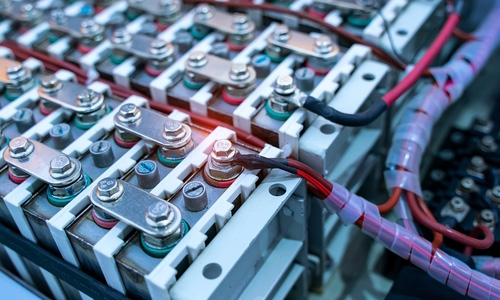
Understanding the Process: Lithium Ion and Battery Production
As the world welcomes in the era of clean-energy economies, batteries will play a very important role. In fact, the lithium battery market is expected to grow 5 to 10 times in the next decade globally.
As a systematic approach to battery production, the Federal Consortium for Advanced Batteries has outlined a blueprint for developing a lithium-battery manufacturing value chain. According to the blueprint, the lithium-battery supply chain–from raw materials production to end-of-life recycling–can be divided into three overarching steps, each with its own specific steps. These are upstream, midstream, and downstream processes.
In our White Paper, Test For Success: Li-ion Battery Minerals Processing & Recycling, we examine the equipment used during the midstream process step and the importance of testing in a laboratory environment.
Steps involved in preparing Lithium ion for Battery Production
UPSTREAM
- This step includes the mining and extraction of lithium and other minerals. Lithium constitutes 0.002% of the earth’s crust and is present in seawater at a concentration of 14-25 ppm. However, high-grade lithium in minable quantities is scarce.
MIDSTREAM PROCESS
- In this step, additional processing for battery-grade materials such as nickel and cobalt is carried out. Mining and acid leaching from spodumene ores can produce a lithium sulfate solution. Similarly, lithium chloride can be produced from brine.
- The next step is cathode/anode powder production, where battery-grade lithium carbonate or lithium hydroxide is extracted from Lithium chloride or lithium sulfate through LiOH Crystallization.
- This is followed by separation and drying, typically via fluid bed dryers, to form battery-grade Lithium hydroxide. This powder agglomeration is carried out using pin mixers, pug mill mixers, disc pelletizers, and rotary drums.
DOWNSTREAM PROCESS
- The downstream process involves manufacturing electrodes and cells. Pack Manufacturing refers to Li-ion battery processing through winding, welding, and filling. Here, the cells are repeatedly charged and discharged, followed by aging before being shipped.
- Li-ion battery recycling is where lithium is reused and recycled after its end-of-life. Recycling is an important step towards sustainability, given the projected use of batteries in the future. In fact, research shows that recycled lithium-ion batteries can perform better than new ones.
Conclusion
Lithium-ion battery production is an increasingly important process driven by applications in EVs, stationary storage, aviation, and even national security. As the world’s storage requirements increase, the world economy will continue to evolve towards a sustainable energy economy. However, this can only be implemented through the mindful use of lithium, which is only present in limited quantities. Recycling will be important in dealing with lithium scarcity and battery disposal challenges.
To tap into the potential of the Li-ion battery market for recycling and production, you need the right equipment.
S. Howes screw conveyors can be used throughout the process for bulk material handling and transport, including thermal heating or cooling conveyors, feeder conveyors, and steep incline conveyors, while our mixers can support and streamline your midstream steps. These include pug mill mixers for the agglomeration of Li and the other mineral compounds that go into Li-ion batteries. Browse through our range of custom mixers and other equipment for use in lithium handling applications and get in touch today!