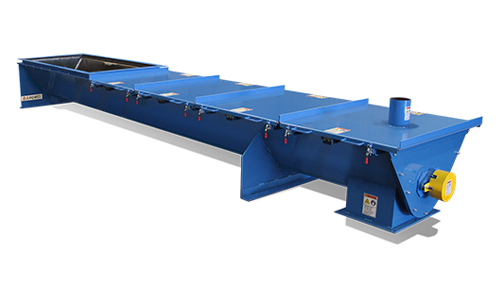
Comparing Cooling Technologies: Mechanical vs. Fluid Bed and Pneumatic Cooling
Many industrial processes require cooling. Effective cooling ensures materials reach desired temperatures for safe handling, storage, or further processing. It also prevents damage to equipment and maintains product integrity. With several cooling technologies available, understanding their differences is critical to making an informed choice.
Overview of Cooling Technologies
Several methods are employed in industries to cool bulk materials:
- Mechanical Thermal Conveyor Systems
- Fluid Bed Cooling
- Pneumatic Cooling
- Dilute Phase Vacuum Conveyor Cooling
- Traditional Screw Conveyors (Open Ambient Cooling)
Each technology has its unique mechanisms, advantages, and limitations.
Mechanical Thermal Conveyor Systems
Mechanical thermal conveyor systems offer a highly efficient and cost-effective method for cooling materials during processing. Using external jackets and hollow main shafts, heated or cooled fluids flow through the conveyor to regulate the material’s temperature. These systems provide indirect heat transfer, ensuring precise control over temperature without direct exposure to fluids, air or gasses.
One of their key advantages is their low operational costs compared to other methods like fluid bed or pneumatic cooling. Mechanical conveyors can adapt to various configurations—like single or multi-screw designs—and are particularly useful in industries where consistent thermal processing is essential. With high-pressure designs, they meet stringent safety standards like the ASME Boiler and Pressure Vessel Code, making them a reliable choice for high-demand high pressure operations.
Fluid Bed Cooling
Fluid bed cooling is a more advanced process where materials are fluidized by forcing air or gas through them, creating a thermal exchange. This method is known for its uniform cooling capabilities because it ensures each material particle is fully exposed to the cooling medium. Usually, fluid beds are used for materials that need quick, consistent cooling.
They excel in fine material handling where mechanical conveyors might struggle. However, they require higher energy consumption and often require more complex installation requirements.
Pneumatic Cooling
Pneumatic cooling employs high-pressure air or gas to carry materials through a system while simultaneously cooling them down. This type of system is well-suited to conveying lightweight or powdered materials across long distances while maintaining temperature control.
Because they rely on fast-moving airflow, pneumatic systems offer rapid cooling but tend to consume more energy than mechanical methods. They are particularly valuable when space is an issue since the system can move materials vertically or over longer distances without occupying much floor space.
Dilute Phase Vacuum Conveyor Cooling
Dilute phase vacuum conveyor cooling relies on moving materials at high velocity through a pipeline under vacuum pressure while applying simultaneous cooling. This method works well for lightweight and fine materials, such as powders or granules, requiring rapid transport and immediate temperature reduction.
Dilute-phase vacuum systems excel in speed but are expensive to operate and maintain due to the energy-intensive vacuum pumps required and the potential wear on system components caused by the fast-moving particles.
Traditional Screw Conveyors (Open Ambient Cooling)
Traditional screw conveyors using open ambient cooling are basic systems that transport materials with minimal temperature regulation by relying solely on ambient air for cooling. While affordable and straightforward in design, they don’t offer much precision or speed in the cooling process. These systems are ideal for applications where exact temperature control isn’t critical, but moving material efficiently still matters.
Given their straightforward nature, traditional screw conveyors have fewer moving parts than fluid bed or pneumatic systems, meaning they require less maintenance but have limited applicability when precise thermal processing is necessary.
Choosing the Right Cooling Technology
Deciding which cooling system suits your process will depend on multiple factors: material type, cooling speed, energy efficiency, space constraints, and budget. If you’re looking for a custom cooling solution, consider exploring S. Howes’ wide range of conveying systems. For more detailed information or to get started on a custom-engineered solution, don’t hesitate to request a quote.