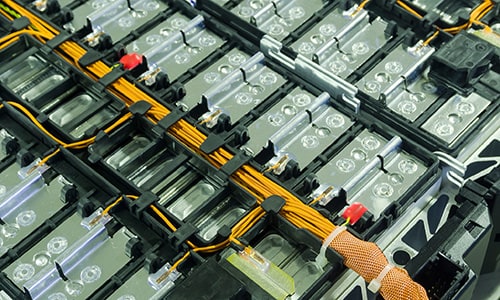
Battery Electrode Slurry: Continuous Mixers vs. Batch Mixers
Lithium-based batteries have become the lifeblood of modern society as the world shifts to eco-friendly power amid the declining use of fossil fuels. With the increasing number of portable devices, EVs, and other applications, the demand for Li-Ion power is estimated to grow from 526 GWh in 2020 to 9300 GWh in 2030.
Now, here’s the thing: the quality of these batteries relies on the battery electrode slurry mixing process. Traditionally, these slurries have been prepared using batch mixers. However, in recent years, continuous mixers have gained traction in this field and are starting to be used more often to produce these slurries. In this blog, we explore how both machines work and compare them so you can decide which is right for you.
The Traditional Process – Batch Mixing
Before we delve into the new approach, let’s look at the most prevalent technique, batch mixing. Batch mixers are somewhat like kitchen mixers used for baking but much larger. The components of the final product are measured out and added into the mixer before the final blended product is discharged from the unit. In this process, slurry components such as active materials, solvents, binders, and additives are blended in a large vessel. Depending on the mixed materials and the required homogeneity level, this process can be quite time-consuming, lasting from 4 to 8 hours. During this period, monitoring the slurry’s progress is challenging due to the constant mixing.
Once the battery electrode slurry is mixed, the slurry is passed through a slot die onto the electrode’s collector foil, followed by drying along lengthy surfaces. The drying allows the solvent to evaporate before the slurry-coated metal foil becomes suitable for battery use.
Thus, while batch mixers create a reliable end product, they take several hours to process. They also require a significant amount of space and energy. Moreover, achieving consistent quality in every batch can be a challenge, leading to variations in battery performance.
Continuous Mixing – A New Approach
Now, enter the game-changer: continuous mixers (aka twin-shafted mixers). These innovative machines are transforming the way slurry mixing is done in the battery industry. Instead of mixing in batches, continuous mixers blend the components continuously, resulting in a uniform slurry.
A continuous mixer has two counter-rotating shafts with paddles in a housing. The material enters the housing, which is then fluidized by the fast-rotating paddles. Then, once the material exits the mixer as a homogeneous blend, it’s passed through a die to mold it. The most significant advantages of continuous mixers are controlling paddle speed, feed rate, and zone temperatures. The results of continuous mixing are impressive, as we will see shortly.
Benefits of Continuous Mixers Over Batch Mixers
So, why should you consider choosing continuous mixers over traditional batch mixers? Here are some compelling reasons:
- Better Speed: Continuous mixers make the slurry move quickly. It vastly reduces the production time and minimizes the risk of contamination.
- Energy and Space Savings: Continuous mixers are compact and scalable. Moreover, twin paddles can combine materials with less or no solvent, significantly reducing drying effort and saving space and energy.
- Cost-Effectiveness: The reduced production time, energy consumption and space requirements translate into cost savings in the long run.
- Enhanced Consistency: The increased agitation produced by continuous mixers helps to produce a consistent product, which leads to better battery performance and quality.
- Improved Dispersion: Higher shear forces and rotational speeds in the mixer create finer particle sizes and better dispersion, reducing clogs in downstream filters.
The Right Equipment for You
Quality slurry leads to quality battery. For lithium-ion battery slurry mixing, continuous mixers are the future. Their speed, space efficiency, and consistency keep you competitive.
We take a look at the supply chain of Electric Vehicle Batteries (EVB’s) and the importance of testing EVB minerals with the equipment used during the Midstream step for processing and recycling the minerals.
At S. Howes, we offer both batch and continuous mixers. Our Simplex and Duplex models for continuous mixing (with patented agitator paddles) are ideal for continuous, homogeneous blending of materials.
With several optional features, the S. Howes’ engineering team can suggest a standard or custom design based on your processing needs.
Contact us to request a quote or learn more about how we can help optimize your industrial processes.