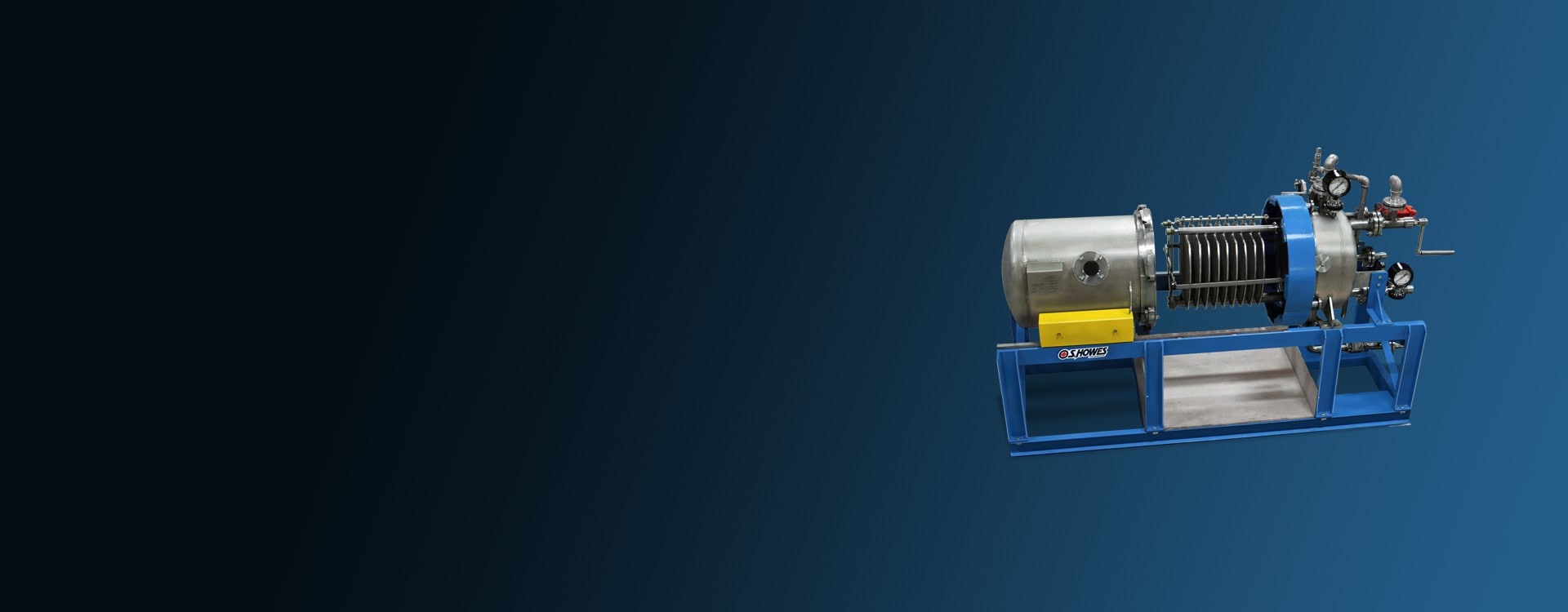
Pressure Leaf Filter
Wet or dry cake pressure leaf filters from S. Howes.
Where liquids/solids separation is required, Howes Pressure Leaf Filters provide either a dry or wet cake discharge for applications requiring flow rates up to roughly 1800 GPM and solids material composition up to 1% (or about 10,000 PPM). These units are ideal for high polish applications where 1/10 micron solids separation is required.
Pressure Leaf Filters provide a constant flow of material that passes through a set of contained leaves that support filter media through a continuously increasing cake layer. The constant flow increases pressure drop across the cake throughout the cycle. Our filters typically use Diatomaceous Earth filter aid as pre-coat and body feed to improve rate and clarity. Depending on the characteristics of the solids, the cake can be discharged either as a wet mass or a dry mass – which in turn determines the discharge design of equipment.
The units can be designed using automated or manual hydraulic shell retraction and are constructed of mild, stainless steel or other exotic alloys.
Pressure Nutsches
Pressure Nutsches are designed with a single leaf and are typically used for easily filtered materials or for lab/pilot applications because of their minimal throughout capacity. Pressure Nutsches provide pressurized or vacuum filtration for low throughput capacity and/or minimum floor space applications. Pressure and temperature can be controlled to accomplish thermal drying or reaction. A single leaf is used for the filter element.
Let our application engineers help you specify the equipment configuration
and leaf designs best suited to your unique processing requirements.
Sample Applications
All filter equipment is custom designed for each application. Equipment is engineered and manufactured at the S. Howes plant in Silver Creek, NY.
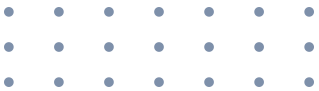
- Acids
- Biofuels
- Breweries and Wineries
- Chlor-Alkali Industry
- Drinking and Waste Water
- Edible Oils
- Fine Chemicals
- Fruit Juices
- Molten Sulphur
- Petrochemicals
- Pharmaceuticals
- Salts and Sugar Processing
Filter Leaf Options
Spotwelded
3-ply construction for the most economical metallic leaf. It consists of a keyhole frame and 4 x 4 mesh drainage member with 24 x 110 P.D.W. screen. The whole system is then spotwelded together.
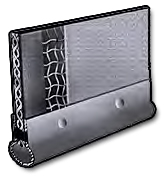
Riveted
3-ply construction consists of a keyhole frame and 4 x 4 mesh drainage member with 24 x 110 P.D.W. screen. This style is riveted together to facilitate screen replacement.

Bolted
3-ply construction consists of a keyhole frame and 4 x 4 mesh drainage member with 24 x 110 P.D.W. screen. The bolted style allows for the quickest, most efficient screen replacement.
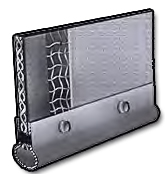
Bag Style
Standard for sluicing filters, this style consists of a keyhole
frame with a tubular slit drainage member. Polypropylene netting is attached to the drainage member and the whole leaf is covered with a fabric bag.
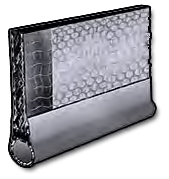
Heavy-Duty (5-Ply)
An intermediate screen of perforated plate has been added to provide a 5-ply, heavy-duty construction.
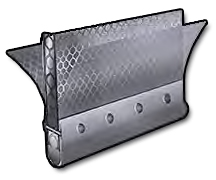
Wet Cake
Where the filtration process produces a wet cake, the Howes Wet Cake Pressure Leaf Filter provides a multiple leaf configuration with an oscillating or hydro jet sluice filtrate discharge mechanism. Both horizontal and vertical tank configurations are available.
Wet Cake Discharge Horizontal Tank Filter (Type HC)
Features
- 36”, 48”, 60”, and 72” diameter vessels with oscillating sluicers
- All leaves are the same size for easy cleaning and inspection
- All piping to stationary front head (no connections to break)
- External wheels for easy, quick tank retraction and simple maintenance
- Waist high frame
- Bolted tank closure
Options
- High profile frame
- Electrically driven hydraulic pump
- Hydraulic shell retraction
- Non-metallic linings
- Automated operation
- Quick open/close tank closure
Wet Cake Discharge Vertical Tank Filter (Type V)
Features
- 18”, 24”, 30”, 36”, 42”, 48”, 54”, and 60” diameter vessels
- Handwheel operated lift cover
- Spacers prevent leaves from rising out of manifold
- No piping connections to break
- Oversized drain for fast discharge of sluiced cake
- Flow pattern across bottom of tank prevents settling
- Inlet baffle for balanced slurry distribution
- Rugged cover closure
- Cover secured with swing bolts and hex nuts
Options
- Hydraulically operated cover lift
- Conical bottom
- Bottom inlet
- Quick opening top cover
Wet Cake Vertical Tank Horizontal Filter (Type VH)
Features
- 18”, 24”, 30”, 36”, 42”, 48”, 54”, and 60” diameter vessels
- Sluice discharge eliminates disassembly time to open the tank
- All leaves are the same for easy cleaning and replacement access
- Eyebolt and hex nut closure
Options
- Optional dry cake discharge removes sluicers – each leaf is individually removed and cleaned
- Tailings outlet
Dry Cake
Where the filtration process produces a dry cake or where sluicing is not feasible, the Howes Dry Cake Pressure Leaf Filter provides a multiple leaf confutation with a large filtration area and solids holding tank. Both horizontal and vertical tank configurations are available.
Dry Cake Discharge Horizontal Tank Filter (Type DHC)
Features
- 36”, 48”, 60”, and 72” diameter vessels
- All leaves are the same size for easy cleaning and inspection access
- Air driven vibrator
- All piping to stationary front head (no connections to break)
- External wheels for easy, quick tank retraction and simple maintenance
- Waist high frame
- Bolted tank closure
Options
- High profile frame
- Electrically driven hydraulic pump
- Hydraulic shell retraction
- Non-metallic linings
- Automated operation
- Quick open/close tank closure
Dry Cake Discharge Vertical Tank Filter (Type DV)
Features
- 18”, 24”, 30”, 36”, 42”, 48”, 54”, and 60” diameter vessels
- Cover secured with swing bolts and hex nuts
- No piping connections to break
- Supported on brackets
- Quick opening discharge
- Full opening bottom for fast cake discharge
- Air driven vibrator for leaf cleaning
- Minimum floor space required
Options
- Quick opening top cover
- Legs or working platform instead of standard support brackets
- Tailings leaf discharge
- External discharge manifold
- Cone bottom discharge
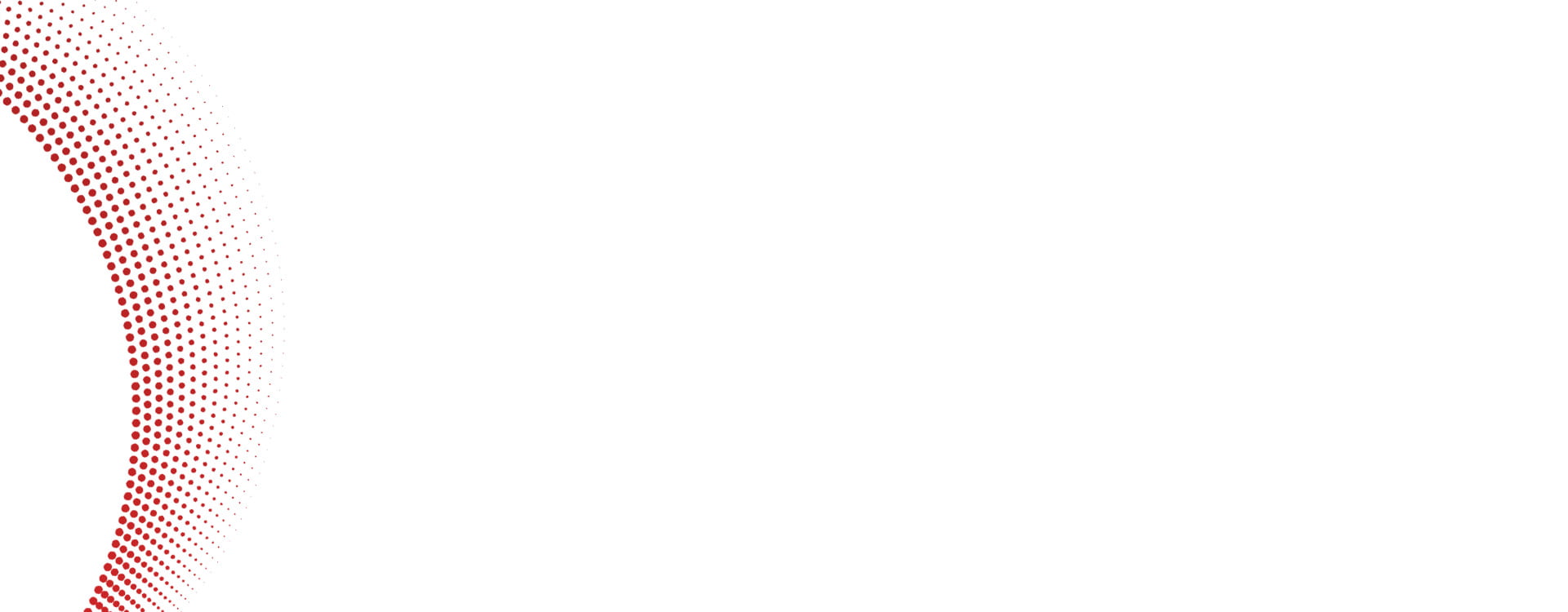
Test Lab & Innovation Center
Your Material Product. Our Thermal Processing Equipment.
Make sure your new process equipment delivers your desired final material requirements.
Lab Testing
Leverage the CPEG Innovation Center and expertise in process engineering to test material product prior to the design or purchase of bulk solids and material handling equipment.
Testing With Rental Units
When material testing in the Innovation Center is not feasible, S. Howes provides rental equipment that can be shipped directly to your site for reliable testing of powder and bulk solids materials.